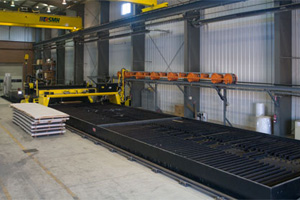
Plasma cutters are methods of precision cutting most ideal for various alloys. Metal precision cutters and metal manipulators like plasma systems help to build structures in which today's society heavily relies on. The abilities of plasma cutting aid in the construction of:
There are plenty of different types of plasma systems. The devices range from small and large scales, portable and stationary, as well as manual and automatic. Despite the varying types, most plasma cutters function the same way.
Plasma cutting systems function on the basis of electrochemistry. The process consists of an inert gas that travels very quickly through an extremely tight channel, forcing the gas to pressurize. The gas passes through a swirl ring, spinning the gas and increasing its speed.
A negatively charged electrode rests in the centre of the channel. This electrode is powered when the plasma nozzle touches the the workpiece, creating a circuit that causes a spark known as the plasma arc or electric arc. The gas traveling through the narrow pathway is turned into plasma, as it reaches temperatures of about 16,600 degrees to 25,000 degrees Celsius (approximately 25,000 to 45,000 degrees Fahrenheit).
The plasma torch exiting the nozzle is surrounded by a shielding gas that helps to control the direction and parameters of the plasma. The shielding gas also ensures that the plasma beam reaches and penetrates the workpiece, as it guides the plasma torch.
Automatic plasma cutters, or CNC plasma cutters, are a popular preference within the precision cutting industry.
CNC, or computer numerical controlled, plasma cutters provide several advantages over manual versions. CNC, also known as LCD plasma systems, are a more preferred tool as they offer better precision and accuracy. As a result, these systems reduce the likelihood of errors and by extension, the need for secondary processing.
CNC plasma cutters employ a hard disk to store different dimensions and specifications of the desired cuts. The computer performs all the necessary calculations and controls the physical task of cutting. CNC plasma cutting limits the probability of human errors and are thereby more efficient in regards to production time and costs.
Plasma gouging systems are another form of the many plasma cutters available. The main difference between plasma cutters and plasma gougers is found in the torch.
In plasma cutting, the purpose is to create a straight, clean, and narrow kerf while producing minimal dross. In plasma gouging, the goal is to produce as much metal removal in volume as possible. The torch then, in a plasma gouger has a much wider and softer arc. In a plasma cutting torch, the arc is significantly more confined and narrow.
All plasma cutting systems consist of consumable parts. These include the:
-
Nozzle
-
Electrode
-
Swirl ring
These pieces of equipment are subject to wear and therefore need repeated maintenance and replacement. Another concerning factor of plasma cutting are heat affected zones, or HAZ's. This refers to the heat used to cut the metals and the ability to warp the integral properties of the material. This leads to issues of sturdiness and strength. However, HAZ's are often very minimal.
While the approach of plasma cutting has some downfalls, it also has many benefits and there are a variety of plasma cutters and torches that help to eliminate the disadvantages. All plasma cutters produce high quality cuts, as well as complex cuts, are safe to operate, and are very efficient, making plasma cutting devices a leading choice within the precision cutting industry.